Some Known Details About Indonesia Furniture Manufacturers
Some Known Details About Indonesia Furniture Manufacturers
Blog Article
4 Easy Facts About Indonesia Furniture Manufacturers Explained
Table of ContentsNot known Facts About Indonesia Furniture ManufacturersThe Facts About Indonesia Furniture Manufacturers UncoveredThe 10-Second Trick For Indonesia Furniture ManufacturersSome Known Details About Indonesia Furniture Manufacturers The Best Strategy To Use For Indonesia Furniture Manufacturers
There are some drawbacks to buying from a furniture maker. A furniture store is a business that markets furniture made by numerous manufacturers.When you purchase from a furniture merchant, you're purchasing a piece of furnishings that's already been made and prepares to be shipped to your home. Among the advantages of buying from a furniture seller is that you can commonly see and touch the item before you buy it.
At BH Furniture, our team believe in setting new standards for excellence in the production of commercial furnishings - Indonesia furniture manufacturers. Our dedication to advancement has led us to embrace advanced automation innovation, changing the method we produce furniture and propelling us to the leading edge of the market. Gone are the days of manual work dominating the manufacturing floor
Our equipment functions flawlessly, guided by the accurate specifications set by our experienced engineers, making sure consistently high-quality outcome. State goodbye to production hold-ups and overtime prices. Our automated systems run tirelessly, 24/7, guaranteeing a constant and undisturbed workflow. This suggests we not just satisfy but go beyond shipment target dates, providing our clients with a degree of integrity that typical production techniques merely can not match.
Indonesia Furniture Manufacturers for Beginners
Our production ability has skyrocketed, allowing us to meet the demands of also the largest projects without compromising on quality. As your companion in commercial furniture options, we can easily scale our outcome to suit your demands, regardless of the range. While traditional manufacturing depends heavily on hands-on labor, our automated systems have significantly decreased our reliance on a huge workforce.
Furnishings production is an intricate process that includes different stages, from creating and material choice to production and assembly. At each stage, there is a possibility of flaws or errors that can endanger the top quality of the end product. To make certain that furniture is of premium quality, furniture suppliers execute top quality control procedures to recognize and fix any type of problems that might occur during production.
The examination procedure should cover various elements, such as setting up, coating, colour, layout, packaging, labelling, and marking. By executing an extensive assessment procedure, makers can guarantee their items fulfill the needed high quality, safety and security, and toughness needs. They also give the adaptability to resolve problems and make modifications prior to completing the end product.
The procedure starts with the basic materials inspection to the final assembly of the furniture. The objective is to guarantee that the items are devoid of defects, safe, and meet the consumer's expectations. Furnishings quality requirements are collections of guidelines and demands for furnishings production. They specify the needed high quality degree of furniture production and cover facets such as safety and security, useful content longevity, toughness, and ecological effect.
The 9-Second Trick For Indonesia Furniture Manufacturers

To ensure their furnishings items can endure different weather elements, consisting of sun, rain, snow, and wind, suppliers have to consider worldwide identified requirements that consist of examinations and screening. Right here are a few of the standards to remember: ASTM F1561-03 is a global conventional created by the American Area of the International Organization for Screening Materials (ASTM).
UL 962 is an international safety requirement developed by Underwriters Laboratories (UL), an independent international supply safety and security solutions firm. The common applies other to home and industrial home furnishings, consisting of outside furniture.

Getting My Indonesia Furniture Manufacturers To Work
It assists to recognize problems in the furniture and examine its performance and conformity with the needed top quality requirements. These samples commonly represent the various kinds of furniture that they create.
This might involve a combination of various examinations, consisting of stamina screening, resilience testing, safety testing, and environmental influence screening. The samples are then checked for numerous quality specifications, such as strength, longevity, safety, and ecological effect. The outcomes are after that examined to identify whether the products satisfy the required top quality standards.
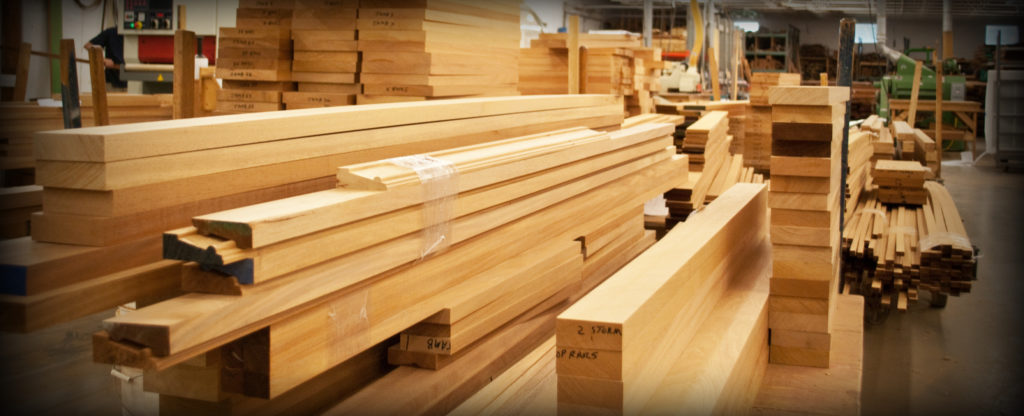
Typically, every retail shop furnishings is various. Layouts conference customer comfort Optimizing space use in storage, display screen, tramp, visitor seating and pathways Making sure simplicity of access to products for tests and purchase Creating modular furniture that is easy to move and recondition her explanation Satisfying security demands of consumers A quick TAT from design to production and installment with marginal errors can help deal with the above worries.
The Definitive Guide for Indonesia Furniture Manufacturers
Likewise, a designer can comprehend the marketplace trends and prepare with innovative layouts in advance. Check out below: Exactly How DriveWorks Aids You to Decrease Lead Time in Production Designers frequently need to alter the shapes and dimensions of furniture at a minute's notification. These might have various visual and practical needs like front desk, and maintenance desk that vary in measurements.
Enhances item quality and decreases scrap. Field guideline documents along with amount departures are likewise generated for retail shop furniture installations. Design iterations and disputes are lowered, and the shop floor can start producing on the day of sales.
It is a highly affordable market, with businesses aiming to maintain up with transforming customer demands and the newest technological trends. Today's consumers are a lot more most likely to prefer furniture that is tailored and made with lasting products.
Report this page